Being in the inventory management business, we run across all sorts of people trying to label all sorts of assets. The biggest problem we see is when people try to print their own barcodes for industrial purposes. Labels are fine for standard office supplies, but for long-term asset identification, they just don’t cut it. We find that by providing pre-printed labels from companies like Metalcraft, our customers are happier and their barcodes read easier. Simply put – they are more reliable, resistant to abuse, stick better, and can outlast the life of your product.
However, even when using these types of labels, we find ourselves fielding questions about why some labels aren’t sticking as well as others. Like many things in life – a little bit of preparation can be hugely beneficial to make certain that you are correctly applying labels. Avoiding common mistakes when applying labels is easy, and trust me, your labels (and your scanners) will thank you in the long run. So, if you’re experiencing problems with your Pressure Sensitive Barcode Labels peeling or falling off after applying them, this is the blog for you!
Help! My Barcode Label Is…
Not Sticking!
While it is important to use the right adhesive for the right surface, most tags will still stick fairly well regardless. If a label is not sticking, the cause is likely something on the surface where you are trying to apply the tag. Oil, water, grease, dirt or any other substance on the surface can all prevent sticking. You might not even notice or see the thin film of oil which is used in the mold process of most plastic part – so be sure to clean the surface well with rubbing alcohol.
If you did clean the surface of application, but did not let the surface dry properly, the edges of your label can start to peel. Patience is key here – give the surface sufficient time to dry after cleaning and avoid sticking any barcodes to any surface that is still wet from a cleaning solution.
Losing its Graphics or Printing!
Too often, people will for one reason or another crease their barcodes down the middle to ease removal from the adhesive or kink a corner. Creasing or kinking is the one sure way to damage the label top and bottom at the same time. Needless to say – avoid doing this at all costs!
Falling Off!
This can be a tricky issue to figure out. There are a few culprits we have discovered that can cause the labels to fall off over time:
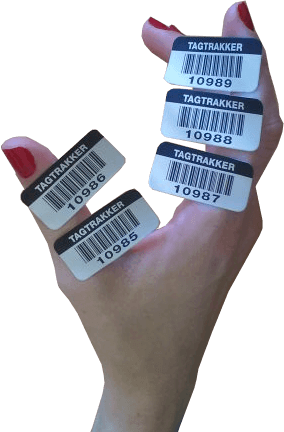
Touching the Adhesive
One of the most common causes is that the person who applied the barcode was touching the adhesive with their fingers without thinking about it. This will get oil on the label and compromise how well it sticks.
Air Bubbles
When a label is attached to a surface, air bubbles can be inadvertently trapped inside the label. To avoid this, we at Telaeris provide a roller with every barcode order for customers to use to push out any excess air bubbles created when applying barcodes.
Textured Surfaces
Customers tend to think that all labels will stick to all surfaces equally well. The fact of the matter is that some textured surfaces are particularly difficult and can require specially made adhesive materials and/or foam to contour to the surface. If you are attaching to a material with a lots of texture, talk to your label company first – you will be happy you did.
Poor Label Storage
Keep your labels in storage under 70 degrees Fahrenheit and 50% humidity. Other environments could damage the adhesive. Check out this blog to see how higher-quality labels withstand extreme temperatures.

Follow these tips and your barcodes will not only last a long time, but they will also reduce future headaches for yourself.
By David Carta, Telaeris CEO & Gloria Toth, Telaeris Engineer
Great article! These are great tips. Another is to consult with a label expert who may suggest a custom label with adhesive that can withstand moisture, extreme temperatures, chemicals and friction.
Very much informative article for understanding the right concept of barcode labels.