Introduction
What is the purpose of this site?
What can be learned here?
- Safety or Security Officer
- Evacuation, Fire, or Floor Captain
- Emergency or Crisis Manager
- Occupational Safety and Health Specialist
- Safety Engineer
- Safety Consultant
- Coordinator of Loss Control
- Safety or Risk Manager
- Certified Safety Professional® (CSP®)
- Safety Management Specialist® (SMS®)
- Associate Safety Professional® (ASP®)
- Occupational Hygiene and Safety Technician® (OHST®)
- Construction Health and Safety Technician® (CHST®)
- Safety Trained Supervisor® (STS®)
- Safety Trained Supervisor Construction® (STSC®)
- Certified Instructional Trainer® (CIT®)
What is NOT included here?
This is neither a business contingency planning nor a network operations resource. This guide is strictly focused on what we have seen works well for effective emergency evacuation, based on our expertise in providing emergency mustering solutions. Please look elsewhere for guidance on network recovery, backup strategies, power failures, money recovery, and/or drafting a business contingency plan. Here are some helpful references:What is an emergency evacuation?
Importance of Planning
How many emergencies happen every year?
Source: U.S. Fire Association (https://www.usfa.fema.gov/statistics/nonresidential-fires/index.html)
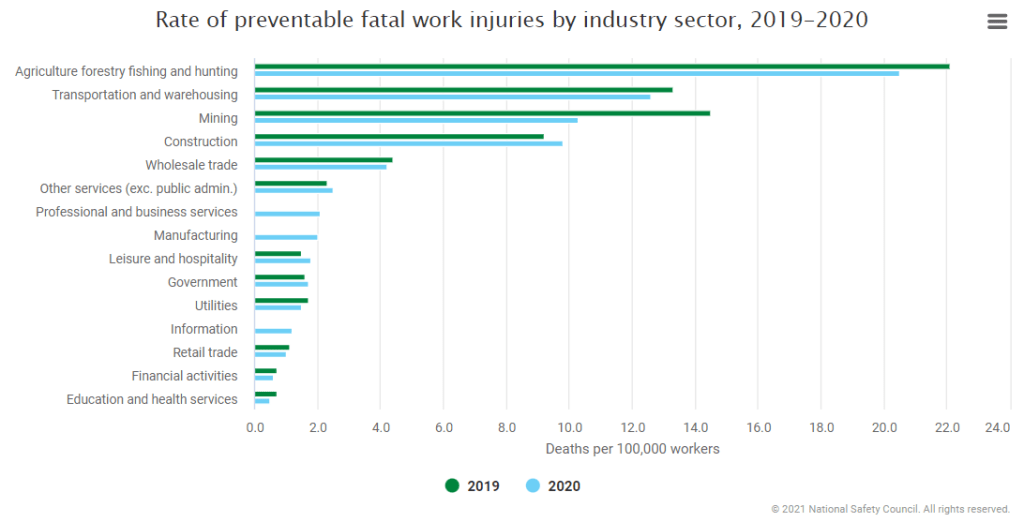
Source: National Safety Council (https://injuryfacts.nsc.org/work/work-overview/work-safety-introduction/)
What types of emergencies require evacuation procedures?
There are a variety of emergencies that may require a workplace to be evacuated, both man-made and natural. These emergencies include:
- Fires
- Explosions
- Power outages
- Earthquakes
- Floods
- Tornadoes
- Hurricanes
- Chemical spills
- Toxic releases
- Gas leaks
- Bomb threats
- Violence
- Terrorism
- Active shooters
Where do emergencies happen?
Who can get injured?
There is no way to tell who will get hurt during an emergency. While some jobs are inherently riskier than others, the reality is that anyone can be injured in an emergency.
Who is liable?
Employers are responsible for the safety of their employees and anyone on their company premises. In the case of larger events, the company may be liable for anyone in the work vicinity. Some companies may have a contract that frees them from certain liability in case an employee gets hurt; however, companies are still responsible for ensuring that everything has been done to ensure worker safety. Without doing so, companies can be deemed negligent.
Employers have a duty of “ordinary or reasonable care” that places a legal obligation to protect their employees from harm while they are under their care, services, or while exposed to work activities.
Please note that by providing this information, it does not place liability on Telaeris, Inc. This is simply a guide to help companies and safety professionals create a more effective EAP. Companies are still responsible for doing the appropriate due diligence in creating and carrying out their specific plans.
Who is financially responsible?
Employers generally pay for the expenses that arise out of emergencies. Depending on the extent of the emergency and any damages, costs can vary from hundreds to billions of dollars. Costs can include damaged buildings or facility repair, worker compensation, medical expenses, and loss of profit. The more time spent not working, the more money employers lose.
According to the National Safety Council (NSC) in 2020, the total workplace injury costs were about $163.9 billion resulting in 4,113 deaths. This breaks down to $1,100 per worker, $1,310,000 per death, and $44,000 per medically consulted injury. The NSC has also estimated that there were close to 100 million days lost due to injuries in 2020 for all the workers that were injured.
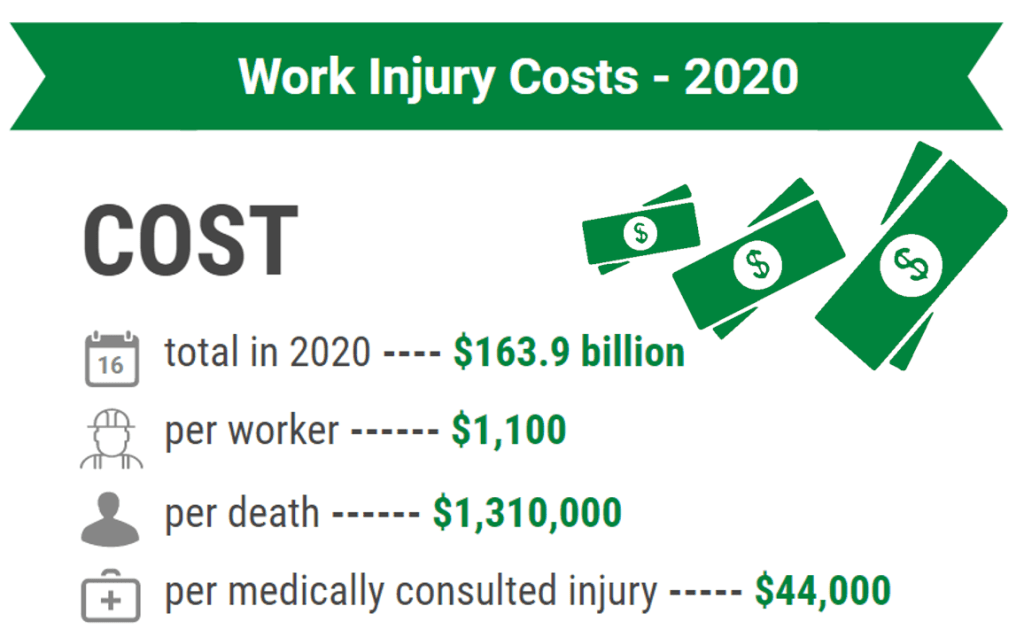
Source: National Safety Council (https://injuryfacts.nsc.org/work/costs/work-injury-costs/)
According to OSHA, in 2018 Liberty Mutual conducted its Workplace Safety Index and found that employers paid over $1 billion every week for disabling, non-fatal injuries that happened in the workplace (https://www.osha.gov/businesscase). That is over $52 billion in a year!
Having an effective EAP can reduce these costs by reducing the likelihood of employees getting hurt.
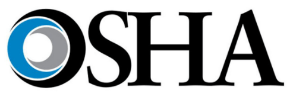
How Does Company Size Affect Preparation?
How should small companies with less than 50 employees plan?
The EAP of a small company with less than 50 employees will be different from the plans of bigger companies. It is easier for smaller companies to keep track of employees and even easier for companies of 30 or less workers because teams can easily see who is accounted for as safely evacuated and who is not. Guidant Financial, a small business financing company, posted a great post (https://www.guidantfinancial.com/blog/small-business-emergency-preparedness/) that outlines some key factors safety professionals should consider when creating an EAP as a small business, including:
- Identify emergency contacts
- Prepare emergency precaution checklists
- Choose safety officer(s)
- Plan evacuation routes
- Clarify shelter-in-place procedures
- Locate Disaster kits
- Arrange continuity planning and technology backups
- Share crisis communication plan
- Designate assembly/mustering area
How should medium sized companies with 50-500 employees plan?
The larger the company, the harder it is to keep track of employees. Employees can be scattered throughout the facility or even off-site. To further complicate things, companies may have multiple buildings, facilities, or sites requiring their own evacuation routes, procedures, and EAP. A more comprehensive plan must be put into place to account for all these concerns. Building upon the key factors that safety professionals should consider when creating an EAP for a small company (see section above), medium-sized companies may need to add more to their EAP, including:
- Create accessible routes for people with disabilities
- Investigate access control system responses to emergencies
- Designate multiple mustering points
- Specify emergency exits and backup exits for each building
- Choose emergency officers and responsibilities
- Identify procedures and tools for accounting for employees and visitors
- Understand how you will track visitors
- Share communication tools to alert employees
How should large sized companies with more than 500 employees plan?
Large companies have the most risk in terms of the number of people who can get injured in an emergency. Building upon the key factors that safety professionals should consider when creating an EAP for small and medium-sized businesses (see section above), large-sized companies may need to add additional factors to the EAP, including:
- How to account for shift changes and off-site workers
- Implement a comprehensive mustering tool that provides real-time information about employee locations
- Purchase and locate protective equipment/supplies for as many people as the facility holds
- Document backup procedures in case your main plan fails
- Identify potential hazards (elevators, stairs, heavy-duty equipment)
- Designate critical employees for shutting off equipment
Preparation – Before an Emergency Event
How to prepare evacuation routes for a facility or building?
The EAP should clearly define the evacuation routes for all workers. There are several specific items that companies should pay particular attention to:
- Ensure Exit Routes are Clear—All evacuation routes and exits should be checked periodically to ensure they are not blocked in any way by equipment or boxes, or are not being inappropriately used as storage. When there is an evacuation, many people will be trying to get out in a hurry. Having anything in the way will not only slow the flow but could be a deadly hazard.
- Evacuation Routes and Exits Must be Clearly Marked – Do not underestimate the importance of marking and making evacuation routes crystal clear. In the event of a power outage, interior spaces could be dark even during the day. In the event of fire or smoke, finding exit doors and stairwells could be difficult due to impaired visibility. All exit doors should be clearly marked and illuminated, and exit signs should be backed up with battery power. Use photoluminescent paint that glows in the dark and have arrows that clearly show evacuation routes visible throughout the facility, including inside corridors, walkways, hallways, and stairwells.
- Clearly Mark Necessary Emergency Equipment – It is also important to clearly mark any emergency equipment which might be needed for an escape, including PPE, oxygen, or tool kits. Also, first aid kits, fire extinguishers, and AEDs should be easy to find when necessary.
How can a facility prepare alarms and employee notifications?
There are various ways to send out alarms and notifications to employees and visitors in the event of an emergency. Every company needs to have at least one method defined.
The most common is a fire alarm system that warns employees and visitors onsite when smoke, fire, carbon monoxide, or another fire-related emergency is detected. Fire alarms can be activated automatically from sensors, such as smoke detectors and heat detectors, or may be manually activated from a call point or pull station. The alarm itself is typically loud with either motorized bells or wall-mountable sounders or horns. Strobe lights may also be used to indicate an alarm as well as automated voice evacuation message warnings to provide occupants instructions, such as not to use elevators. All fire alarm systems should be appropriately backed by a battery system and should be checked periodically.
Notification systems range from SMS, email, overhead speakers, phone calls, etc. Two-way systems exist enabling safety professionals to send out the notification and receive responses from employees. Web applications and mobile applications exist which provide the ability for the company roster to be maintained and viewed. This can additionally be connected to the physical access control system or time and attendance system to identify employees onsite. It is recommended to have a system that collects real-time data during an emergency event that accounts for employees and visitors as safely evacuated when reaching the assembly area or mustering point.
It is also important to test the alarm and notification system to ensure that it works properly. Having the alarm system fail during an actual emergency could have devastating effects. An EAP should include periodically scheduled tests of the alarm and notification system so that it works appropriately during regularly scheduled drills
What emergency phone numbers should be documented?
In a real emergency event, it is easy to forget even the most well-known information. Therefore, it is recommended to document all the following phone numbers and have them easily available to anyone:
- Fire department
- Paramedics/ local hospital
- Police
- Security office
- Building manager
- Electric Utility
- Water Utility
- Gas Utility
- Employees’ emergency contacts
What equipment and supplies should be prepared in case of an emergency evacuation?
Safety professionals should consider preparing kits with emergency equipment and supplies in case of a workplace emergency. These should be made easily accessible in case of an evacuation. A designated safety professional should make sure that all supplies in the kit remain useable and up to date. In addition, safety professionals can encourage employees to keep personal emergency kits in their work area or in their cars (if available), provided that personal kits do not cause safety issues.
Below is a small list of emergency equipment and supplies that can be useful in any type of emergency. Please note that depending on the emergency and size of company, some of these items may not be used at all or more may be needed than what is listed here.
- Food
- Water
- Medications
- First aid kit
- Petty cash
- Toiletries
- Dust masks
- Cleaning supplies
- Toilet paper
- Duct tape
- Gloves
- Garbage bags and twist ties
- Fire hydrant wrench
- Gas shutoff tool
- Battery powered radios
- Flashlights with extra batteries
Resources:
https://www.ready.pa.gov/BePrepared/BuildKit/Pages/For-The-Workplace.aspx
https://www.guidantfinancial.com/blog/small-business-emergency-preparedness/
What other workplace hazards exist?
There are potential hazards all around. It is important to be aware of the potential hazards in your workplace because they can adversely affect or exacerbate emergencies. Potential hazards include:
- Corrosives such as sulfuric acid, halogen gases, etc.
- Corrosive materials such as steel, aluminum, and other inorganic material that react with corrosives
- Irritants such as ammonia, chlorine, ozone, nitrous oxide, etc.
- Toxic materials such as gasoline, acetone, etc.
- Flammable and combustible liquids
- Compressed gases
This is not a comprehensive list of all the potential hazards; however, it is critical to look and think of the things around the workplace that can be dangerous during an emergency. There should be precautions in place that will provide safety despite these items being around. For example, in chemistry classrooms, there are usually showers or eye baths in case of chemical exposure. On construction sites, there are usually (orange) signs that read “Warning” or “Caution” to warn workers of hazards or dangerous objects. These are simple precautions that can lessen the impact of emergencies.
Where should facilities locate assembly areas / mustering points?
First and foremost, assembly areas / mustering points need to be positioned far enough away from danger to be safe. Dangers include the collapsing of a wall, structure, overhead power lines, traffic, or hazardous terrain. A minimum distance of 1.5 times the height of the wall or structure is recommended. Depending on the workplace, assembly areas / mustering points should also have adequate airflow in case of fire and smoke. Consider normal wind directions and alternative assembly areas / mustering points in the event of a wind change. Assembly areas / mustering points should be easily accessible and in a high visibility area so that safety professionals and first responders can see what is happening even if communications are lost. There should be enough assembly areas / mustering points to accommodate all employees and visitors on site and positioned in locations that will not interfere with first responders and emergency vehicles/equipment. It is important assembly areas / mustering points are clearly marked with signage mounted high enough so they cannot be obstructed by vehicles or other moving objects.
Resource:
https://www.safeopedia.com/top-10-things-you-should-know-about-muster-points/2/6289
What type of evacuation is appropriate for an emergency event?
Safety professionals need to assess each emergency event and the appropriate evacuation. Some questions to consider:
- What kind of emergency is it?
- Is evacuation necessary?
- Is it safe to exit the building?
- Is it safe to stay inside?
- Is sheltering in place the best option?
- How close are the emergency exits?
- Will first responders be able to reach the site?
- Who should be contacted?
Depending on where the workplace is located, there may be predetermined building safety requirements. For example, if the workplace is in an area susceptible to tornadoes, the building may already have a basement to shelter in place which is safer than evacuating in that case. It is important for safety professions to plan and direct employees and visitors with the best course of action including:
- Evacuate onsite to a designated assembly area / mustering point. This is the most common type of emergency evacuation.
- Evacuate offsite to a designated assembly area(s) / mustering point(s). This is typical for larger industrial complexes.
- Shelter in place – typical for tornadoes, hurricanes, and human-caused dangers.
- Moved assembly area / mustering point – typical with smoke or gas leaks and changes in wind direction.
How should employers train and educate employees?
EAP education and training is important. Employee education and training for emergency procedures can take the form of employee packets, meetings or classes, videos, and practice drills. Start by providing employees with a copy of the EAP and showing them the emergency exits. Reinforce education and training by requiring employees to go through a course that teaches and tests knowledge of the company EAP. Then regularly practice their knowledge by doing drills and look for opportunities to improve the plan. The point is to provide employees with general knowledge of what to do in case of an emergency. The more education and training, the more the employees will know what to do, making it easier to evacuate during a real emergency. Employers should do everything possible to make sure employees are safe.
The National Safety Council offers training courses online at a cost. In-person training and on-site consulting is also available and can be a great resource for those who do not wish to create their own EAP from scratch. The National Safety Council is a nonprofit organization focusing on safety awareness and training in the workplace, roads, and communities.
The National Association of Safety Professionals (NASP) also has online and live courses. The NASP provides safety certificates to employers upon course completion for workplace safety.
How important are fire drills?
Fire drills are probably one of the most commonly practiced safety drills because fires can happen anywhere. Fire drills are the most basic evacuation drills. Implemented properly, fire drills can demonstrate the strengths and weaknesses of the EAP. Fire drills should be practiced frequently throughout the year. Doing so helps safety professionals ensure that the alarm system, EAP, evacuation routes, and equipment work properly during a real emergency. All workplaces are constantly in flux due to environmental, operational, and physical changes that happen throughout the year. Safety professionals want to make sure the EAP works despite these changes and updates.
How should a facility prepare a chain of command and important personnel for emergencies?
During an emergency it may be difficult to know who to listen to specially when there is panic and confusion. Generally, there is a chain of command that should be followed. At the top of every chain of command should be First Responders. First Responders are experts, and it is essential to follow their instructions.
Here is a sample chain of command for small companies with less than 50 people:
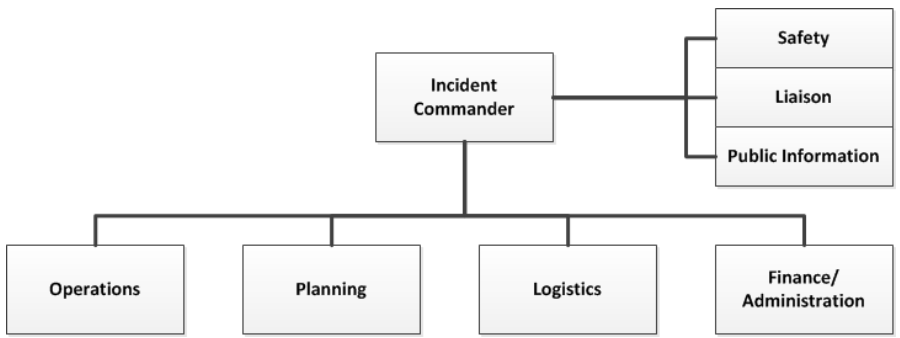
Source: Ready.gov (https://www.ready.gov/incident-management)
This chart is a very simple outline of the different points of contact that may be essential in the chain of command. Here is a breakdown of the different responsibilities of each person/department:
- Incident Commander (Emergency Response Officer) – The individual in charge of on-site response. Assesses the incident and notifies necessary agencies, departments, and people. Appoints incident command positions as necessary and maintains command.
- Safety – Identifies hazards and prevents accidents, prepares safety plans and ensures they are communicated with employees, prevents unsafe acts and conditions.
- Liaison – Main point of contact for outside organizations and companies, monitors operations.
- Public Information – Notifies crisis communication team, serves as a spokesperson, deals with the release of information to the media.
- Operations – In charge of managing all tactical operations during emergencies, ensures safety of all responses, and expedites any changes to emergency plans.
- Planning – Supervises the planning of EAPs, coordinates with other management teams, assembles information for alternative plans, assesses impact on people and environment, creates incident status information.
- Logistics – Handles and provides resources (supplies, workspace, transportation, equipment, etc.) to stabilize incident personnel and provides input for incident EAP.
- Finance/administration – Manages financial aspects of incidents, handles damages, liability, and injury claims, tracks worker time and costs for materials and supplies, and coordinates with logistics team.
Below is a sample chain of command from the University of California in Los Angeles for large sized companies with more than 500 people:
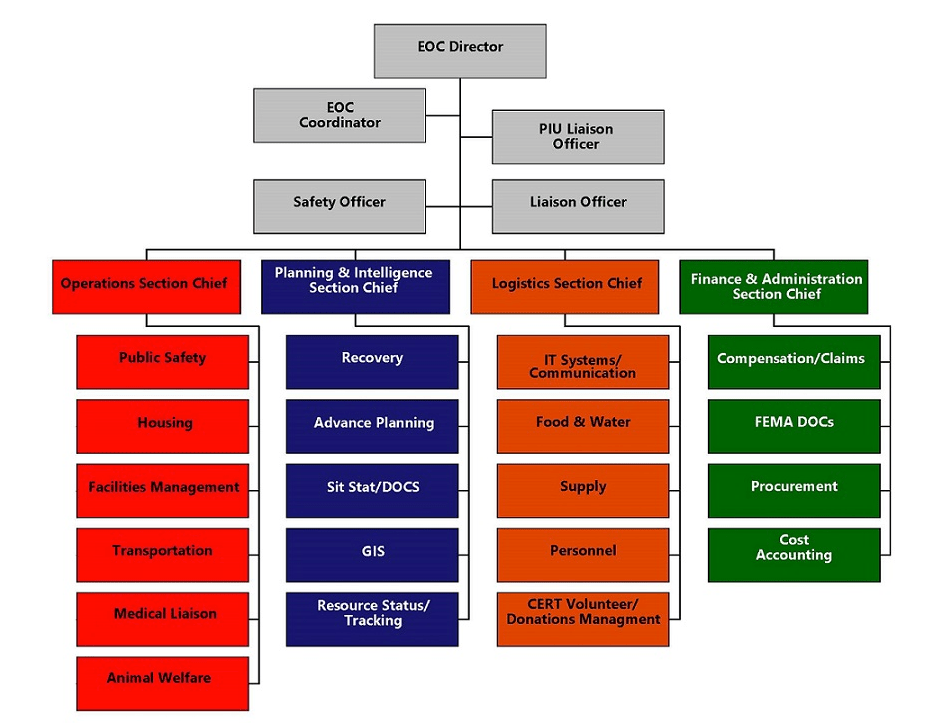
Chain of commands differ depending on the company including type of facility, number of employees, departments, and type of industry.
What are the minimum OSHA EAP requirements?
According to the Occupational Health & Safety Administration (OSHA), the EAP must include but is not limited to the minimal items below:
- Means of reporting fires and other emergencies
- Evacuation procedures and emergency escape route assignments
- Procedures for employees who remain to operate critical plant operations before they evacuate
- Accounting for all employees after an emergency evacuation has been completed (similarly, the Health and Safety Executive, Britain’s national regulator for workplace health & safety, says that employers are responsible to 'ensure that all personnel are accounted for' in an emergency)
- Rescue and medical duties for employees performing them
- Names or job titles of persons who can be contacted
Reference: https://www.osha.gov/etools/evacuation-plans-procedures/eap/minimum-requirements
What additional information should be included in an EAP?
While the OSHA minimum is a good start, we suggest the additional items be included in a company EAP which is provided to your employees:
- Copies of your established evacuation plan
- Clearly marked evacuation routes
- Assigned assembly areas / mustering points
- A list of emergency contacts
- A roster and/or a device with an electronic list to account for all your employees
- Necessary emergency supplies/equipment
- Procedures and people to shut down critical equipment
- Documented ways to alert first responders
- Appropriate alarms and methods to alert employees of danger
During Emergency Evacuation
What is the difference between drills and real emergency evacuations?
Drills and real emergencies are clearly different. There is no way of telling when or what will happen in a real emergency. On the other hand, drills are typically planned and a perfect time to practice the EAP, including accounting for everyone as safely evacuated.
The problem with drills is that they are often not taken seriously. There are employees who do not listen or pay attention during the evacuation process. There are employees who disappear and go off-site. There are employees who ignore the drills and remain in their offices because they view their work as more important than the drill. Unfortunately, in too many cases, drills are not taken seriously due to the lack of real danger. This is a problem because when there is an actual emergency, employees will not know what to do. Companies have to require that employees take drills seriously. Drills should be mandatory, practiced regularly, metrics should be collected, and the EAP should be evaluated for improvements.
Where do real emergency evacuations go wrong?
There are a countless number of variables that can negatively impact a real emergency evacuation. Clearly, some cannot be planned for because of the emergency event itself, such as a fire or explosion blocking egress routes. However, for the workers and visitors who can get out, the following are the typical reasons why emergency evacuations go wrong:
- Employees are unaware of the plan
- Employees do not pay attention during practice drills
- Employees do not listen to the emergency managers
- Employees go missing or wander off
- Alarm and communication systems can fail
- Safety and emergency equipment can fail
How can facilities handle critical plant operations?
Some employees may be required to stay behind temporarily because certain equipment or processes cannot be shut down immediately and must shut down in stages over time. In other cases, with large manufacturers with complex processes, it may not possible to shut down at all in an emergency and some employees need to stay behind to continue operation. In smaller operations, employees may be required to operate fire extinguishers or shut down gas and/or electrical systems and other special equipment. This may include equipment that could be damaged if left operating or create additional hazards to emergency responders, such as releasing hazardous materials. In general, however, employees should leave fighting fires and rescue operations to experts and first responders! In larger operations, security or safety personnel will remain on-site to monitor cameras and access control systems and ensure that everyone has gotten out safely.
It is important that companies review their operations and develop comprehensive and detailed procedures for each specific employee's job. In addition, critical employees need to be trained when to abandon the operation or task and evacuate before their lives become in danger.
Is it always necessary to report an emergency evacuation?
Emergency situations should be reported as soon as possible. Calling 9-1-1 is one common method of reporting emergencies. Contacting the fire department, hospitals, or any other relevant departments depending on the situation are also options. Alarm systems, such as fire alarms, are also required to alert everyone on site.
Reporting requires telling the dispatcher the location, contact information, who is in danger, the nature of the emergency, and if people in the vicinity of the reporter are in danger. It is very important to listen to the instructions of the dispatcher on the phone. Do not hang up until instructed to. Answer their questions quickly and as accurately as possible.
How important are first responders?
9-1-1 should be the first call. First responders, including law enforcement, medics, and firefighters, will dispatch personnel and resources to the emergency area as soon as possible. They will want to know the results of any headcount performed and identify if anyone is not safely accounted for. Their focus will be to help any missing people who could be in danger.
How should facilities prepare to account for employees?
The most important part of emergency evacuation planning is having a reliable and effective way to account for employees and visitors. Telaeris, Inc. has a blog post that talks about 7 different ways you can account for your employees during an emergency.
Accounting for employees and visitors can be accomplished in many ways. The traditional way is with a clipboard and paper roster. The problem with that approach is that it is very time consuming, especially for large companies, and the paper rosters will likely not have the latest occupancy information. Every moment counts in an emergency, and doing roll call this way wastes time and resources when other tasks, such as looking for missing personnel or handing out safety equipment, need to be done as soon as possible. Roll calls also have the disadvantage of missing people who check in at the wrong assembly area, so to get a full view of who is safely evacuated, it requires collecting all the rosters from every evacuation area.
There are other ways to account for employees and visitors much faster. There are communication-oriented applications that enable safety professionals to send out messages or email alerts and receive responses back. Depending on the solution, these responses can be used to account for who is safe and who is missing, collecting all information on a central system. There are also wireless devices that can identify employees at muster sites during an emergency. For example, XPressEntry Handheld Badge and Biometric Readers can quickly account for hundreds or even thousands of people in minutes from anywhere. Other wireless solutions include Real Time Location Tracking (RTLS) systems based on battery-powered RF transponders that track the live location of every employee. Depending on your facility and workspace hazards, one solution might be more appropriate than others.
How important is an employee and visitor roster?
In a real emergency evacuation, anyone can go missing. Emergencies are unpredictable and anyone may neglect to follow directions or go to the wrong assembly area / mustering point. You often don’t know if employees or visitors are trapped in dangerous buildings or if they just decided to leave the site when the emergency began.
Having an accurate roster is very important to know who is truly missing. Smaller companies should always keep the company roster up to date whenever someone joins or leaves the company. Having an accurate list of names of everyone that is on site is important to get an accurate headcount.
Most medium to large companies use an access control system for physical security. This system tracks employee entry and sometimes exit activities. To keep track of the latest occupancy information in real-time generally requires purchase of a third-party tool to provide an up-to-date roster based on this activity. Regardless of the company size, it is wise to invest in an emergency mustering tool that can provide a fast, efficient, and accurate method of accounting for employees and visitors in an evacuation. An example of this is the XPressEntry Handheld Badge and Biometric Reader mentioned above, which connects to the access control system and maintains the latest occupancy information based on live entries into and exit from the facility. A system like this is the best option for an accurate roster.
Without an accurate headcount, employees and visitors are in danger of not being accounted for in an emergency. If there is an employee that came to work that day and goes missing but is not on list, nobody would ever know. It would be difficult to determine their location and if they are safe. It is paramount to identify and find all missing people onsite. First responders will ask your onsite evacuation captions who is missing and will attempt to look for these people in the last place they were seen, potentially putting themselves in harm’s way. But if this information is unknown, first responders cannot help missing employees, leaving the company potentially liable and negligent if anything happens to their employee during the emergency.
When should a company decide to move an evacuation site to a backup location?
There may be times when muster areas or assembly points are in the direct path of destruction or may become unsafe. In these instances, moving the evacuation location for employees will be required, and having procedures in place for this is very important. If you are concerned with a gas or chemical leak, having alternative locations and knowledge of wind direction is critical, as wind can blow a toxic cloud over an assembly area / mustering point.
It is important for safety professionals to know the area and stay updated on the latest weather reports, traffic situations, and other hazards that may affect the evacuation. Subscribing to the local news, government updates, and checking the news online are good resources. For example, in areas where there are hurricanes, safety professionals want to be aware of how intense an approaching hurricane is, if the roads are congested, and if the hurricane is within proximity of the worksite. If it is unsafe to shelter in place, first responders and law enforcement may issue evacuation orders which may override your company EAP. By being prepared with information and resources, you can help keep your employees safe by having them go to the correct assembly area / mustering point or shelter in place, as the situation warrants.
Safety professionals should always have important phone numbers, tools, and information required to account for employees and visitors. Losing track of employees and visitors in an evacuation while moving the assembly area / mustering point is bad business. Even though employees may be tempted to run home to their families, it is important that they first report to safe evacuation locations to be counted.
After an Emergency Evacuation or Drill
What metrics are important to measure during an emergency evacuation or drill?
Metrics are used measure success and drive improvements in the EAP. Evaluating the metrics after an evacuation or drill will lead to faster reaction times and an EAP that is more reliable and trusted by stakeholders. The following is a list of important metrics to collect:
- What was the total number of employees and visitors that were onsite before the emergency?
- How long did it take to detect the emergency and sound the alarm?
- How long did it take to call 9-1-1?
- How many employees and visitors were accounted for at the assembly areas / mustering points?
- How many employees and visitors were not accounted for that were onsite earlier in the day?
- How long did it take to get a full headcount?
- How long did it take first responders to arrive?
- How long did the evacuation take?
- How many injuries were reported?
- How many safety professionals/employees were helping to manage the emergency evacuation?
- What mistakes did the safety professionals report that could be corrected?
How is post-event information used for improvements?
Post-event information is critical to maximizing efficiency and safety. The longer it takes to finish an evacuation and account for employees and visitors, the higher the risk of someone getting hurt. Harvesting metrics during drills and collecting the same type of information in evacuations will generate very useful data that can be analyzed to find areas of improvement. Whether it is an improvement in time or headcount efficiency, this information can help safety professionals adjust the EAP. Even small adjustments can make the EAP incrementally better and enhance safety.
What post-emergency regulatory reporting is required?
Post-emergency reporting requirements depend on a lot of variables. Any oil, chemical, radiological, biological and etiological discharges into the environment, anywhere in the United States and its territories must be reported to the EPA’s National Response Center (https://www.epa.gov/emergency-response/national-response-center). OSHA requires employers to report in-patient hospitalization, amputation, or eye loss within 24 hours, and a fatality must be reported within 8 hours (https://www.osha.gov/report). Make sure to check with state and local government reporting requirements.
Conclusion
A lot goes into developing an EAP and it is well worth the investment of company time and resources to do it right. The National Safety Council (NSC) says that employers who show they care about the safety of their employees see improved morale, increased productivity, lower costs, and fewer injuries. Saving lives and minimizing injury should be priority number one for every employer and making that abundantly clear to employees goes a long way. Start today developing a new EAP or revising an existing EAP to find areas of improvement. Practice fire drills and evacuations regularly. Educate employees and reinforce the importance of the EAP into company culture.
How long should an emergency evacuation take?
There are a lot of factors that influence the time it takes to complete an emergency evacuation. Companies with 500+ employees average 30 minutes from alarm to final muster count using old, traditional paper rosters. Most of that time is consumed accounting for employees and visitors at the assembly areas / mustering points to make sure that everyone safely evacuated. Using wireless devices such as XPressEntry Handheld Badge and Biometric Readers mentioned above can cut that time down significantly. Telaeris, Inc. recommends one (1) XPressEntry device for every 200-250 people to complete a mustering event in 10 minutes or less. In a real emergency evacuation, every second counts to help save lives.
What are the best practices?
- Create and share your company EAP
- Coordinate with emergency services
- Assign evacuation routes and assembly areas / mustering points
- Account for all employees after an emergency evacuation
- Designate an emergency response team
- Provide all employees with copies of the EAP
- Have the right tools / equipment nearby
- Keep it simple
- Protect every individual in your facility
- Conduct evacuation drills
- Work on continuous improvement of your EAP
What are some helpful resources to help create an EAP?
- Planning and Responding to Workplace Emergencies (OSHA)
- How to Plan for Workplace Emergencies and Evacuation
- Family Emergency Preparedness Plan
- National Safety Council
- U.S Fire Administration
- Society for Human Resource Management (SHRM) Emergency Evacuation Procedures
- Ready.gov Evacuation
- Iowa State University Environmental Health and Safety Evacuation Procedures
What are some emergency organizations in the United States?
- FEMA (Federal Emergency Management Association)
- American Red Cross
- NRT (U.S. National Response Team)
- National VOAD (National Voluntary Organization Active in Disaster)
- CDCP (Centers for Disease Control and Prevention)
- CERT (Community Emergency Response Team)
- NDMS (National Disaster Medical System)
- EMAC (Emergency Management Assistance Compact)
- IPAWS (Integrated Public Alert and Warning System)
What are some emergency organizations in the United Kingdom?
- Health and Safety Executive (Britain’s national regulator for workplace health and safety)
- British Red Cross
- EmergencyUK
- UKEMT (UK Emergency Medical Team)
- HI (Humanity & Inclusion)
- DEC (Disaster Emergency Committee)
- Rapid UK
- RedR
- RE:ACT Disaster Response
What are some emergency organizations in Europe?
What are some international emergency organizations?
- International Red Cross
- IRC (International Rescue Committee)
- OCHA (United Nations Office for the Coordination of Humanitarian Affairs)
- USAID (U.S. Foreign Disaster Assistance)
- Project HOPE
- UNDAC (United Nations Disaster Assessment and Coordination)
- WFP (World Food Programme)
- WHO (World Health Organization)
- IEMO (International Emergency Management Organization)
- Direct Relief
- List of International Relief Organizations