
There are lots of hidden costs to doing business, but one you may not think about is the cost of having your employees wait. Waiting for slow computers to boot up, waiting on slow business processes, or what I am going to focus on in this week’s blog – waiting in lines.
Waiting in lines is particularly nasty because not only is your time wasted, but everyone behind you has to wait this additional time as well.
The case that inspired this article involved a client of ours who has a large number of contractors. Every day they wait in long lines to get their tools before going to their job sites. This client asked us to help him speed up the tool checkout process with our software. Together, we listed how waiting in lines negatively affected his bottom line to build internal support for implementing a solution.
Here is a modified version of that list that should apply to most businesses:
- Companies still need to pay their employees while standing around in lines.
- While employees are in lines, they are not being productive for a company. For example, the time on the job for a construction worker goes down with time waiting in line.
- If employees waiting in lines are repairing a manufacturing process, production will be offline longer reducing income.
- Long lines may cause a company to hire more people or build more infrastructure to more quickly process the line. Think about checkout registers at grocery stores.
- Long lines can be a source of dissatisfaction (*see QLess note at bottom of blog). External customers may take their business elsewhere. For your employees (internal customers) it may cause unnecessary job related stress.
- There may be human costs if you are working in an emergency situation such as an evacuation.
Points 2-5 will vary for every business and point 6 has additional concerns related to safety. However, item 1 is simply a matter of math. You can calculate the total savings based on the reduction in time for each person in the line.
I personally find it more intuitive to look at actual examples of the how much money can be saved by reducing wait times. Below is a table for the savings of reducing two seconds from each person’s wait time in a line, for a variety number of employees that might wait in a line. It is surprising to note how fast the savings increase with the number of employees.
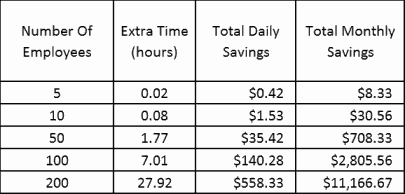
You can download the Excel workbook for this table here.
Back to our specific client’s case. (Shameless plug warning!) By implementing our XPressTools Inventory Management System, tuned to optimize their requirements, we conservatively saved our client 10 seconds for each of his 250 workers when they reached the front of the line. When we plugged in the rest of this client’s numbers into our worksheet, the raw manpower dollar savings per month showed to be close to $200,000.00!
This number did not include other significant savings realized by getting this manufacturing back online faster. With all of this information and a clear ROI for the project, implementing our solution not only made sense but saved a lot of cents as well.
* QLess has an interesting blog and software for dealing with lines.
We have no relationship nor financial interest in QLess.
Comments are closed.
Leave A Comment