There is a quote on the internet, misattributed to Bill Gates, saying, “I will always choose a lazy person to do a difficult job, because he will find an easy way to do it.”
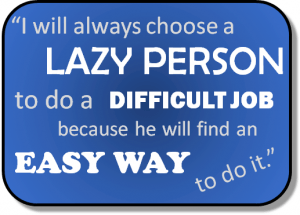
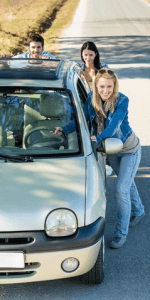
A couple of years ago, Telaeris was awarded a contract with the Marine Corps at Camp Pendleton. They needed to perform a physical inventory of tens of thousands of assets across their 125,000-acre base. These included computer equipment, furniture, weapons, vesicles, and more. We were brought in under a fixed-price contract to augment their manpower specifically to complete the project.
The marine inventory process was simple but slow. From day one, our employees went out in groups of 4-6 to a site, had to locate an item on a list, find its corresponding label number, locate the label in a massive stack, scan the label, and then assign it to the asset…..phew! That put me out of breath just typing all that.
This was the actual process.
- Print out list of assets and hundreds of barcode labels for an area
- Drive to the area with 4-6 people
- Find an asset on the list
- Have one person try to find old label or serial number sticker.
- Disassemble whatever might be needed to access the label.
- Read the number out loud
- Look through the hundreds of printed labels to find the number
- Stick barcode label to asset
- Check item off the list
- Make new lists for assets not found or assets found not on the list
- Repeat for all assets on site
- At end of day, manually transcribe the lists for back-end database update
- Drive out next day to same area to complete newly found assets
Adding our people to their team increased the rate incrementally. Fortunately for Camp Pendleton, our logistics team was backed by our engineering group! After taking time to understand the government process and requirements, the Telaeris engineering team sprung into action.
The Making of a Super Hero
Telaeris engineers built a hardware and software solution called XPressLabels that led to a much faster process. These were the new steps:
- Upload asset list to a tablet computer
- One marine would drive one Telaeris employee to area
- Asset would be found
- Old asset labels were scanned by barcode reader into tablet
- Tablet would print new label using battery powered wireless printer
- Stick barcode label to asset
- Repeat for each asset
The new process allowed one person to do the same job as 6 in about a quarter of the time. Since tags were printed onsite, newly discovered assets could be tagged as well. As all the data was stored electronically, it additionally removed significant data entry at the end of the day.
The biggest surprise we saw from this was the change in the reactions from each government employee as their day was interrupted by the asset management team. With the old system, an office worker would have their office invaded by 6 people who were standing around for 15 minutes, most of the time doing nothing. If a TV needed to be removed from a wall to read an asset label, it could take 30 minutes. This would result in the inevitable jokes about “Yep – good old tax dollars at work!” The Marines would feel it too, knowing that for the most part, the whole system was inefficient.
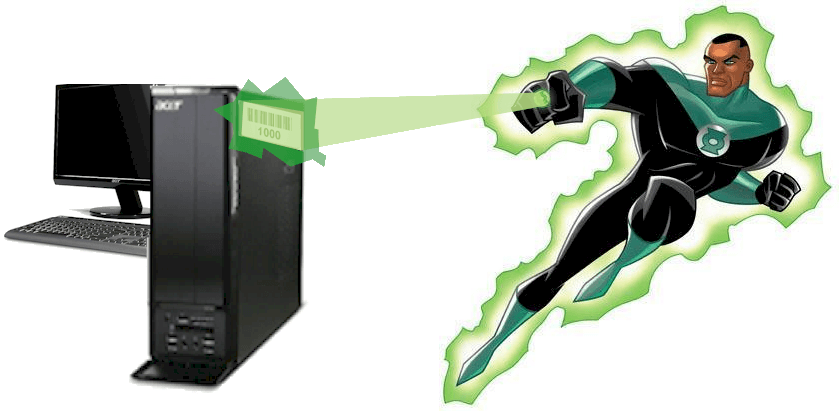
What a change when the new system was introduced!
Our employee Fred described it like this. He would step out into an office and introduce himself. He was carrying a satchel with the label printer and a tablet. On his hand, he had a tiny finger-mounted barcode reader that fit like a ring. Fred would go from one asset to the next, shooting a glowing light from his finger barcode reader, looking to all the world like he had Green Lantern’s power ring. After each scan, Fred would reach into his satchel and pull out the freshly printed label. Usually, he would be done with an office in under 5 minutes, to the amazement of the office occupants, who were disappointed that the interruption wasn’t even long enough for a coffee break.
No standing around, no disparaging comments, and no need to take equipment off the walls! And, he could reach behind the television sets and scan the old label. People actually commented that they were pleasantly surprised that the government could be so efficient. The Marines were proud as well – they felt they were being efficient and productive.
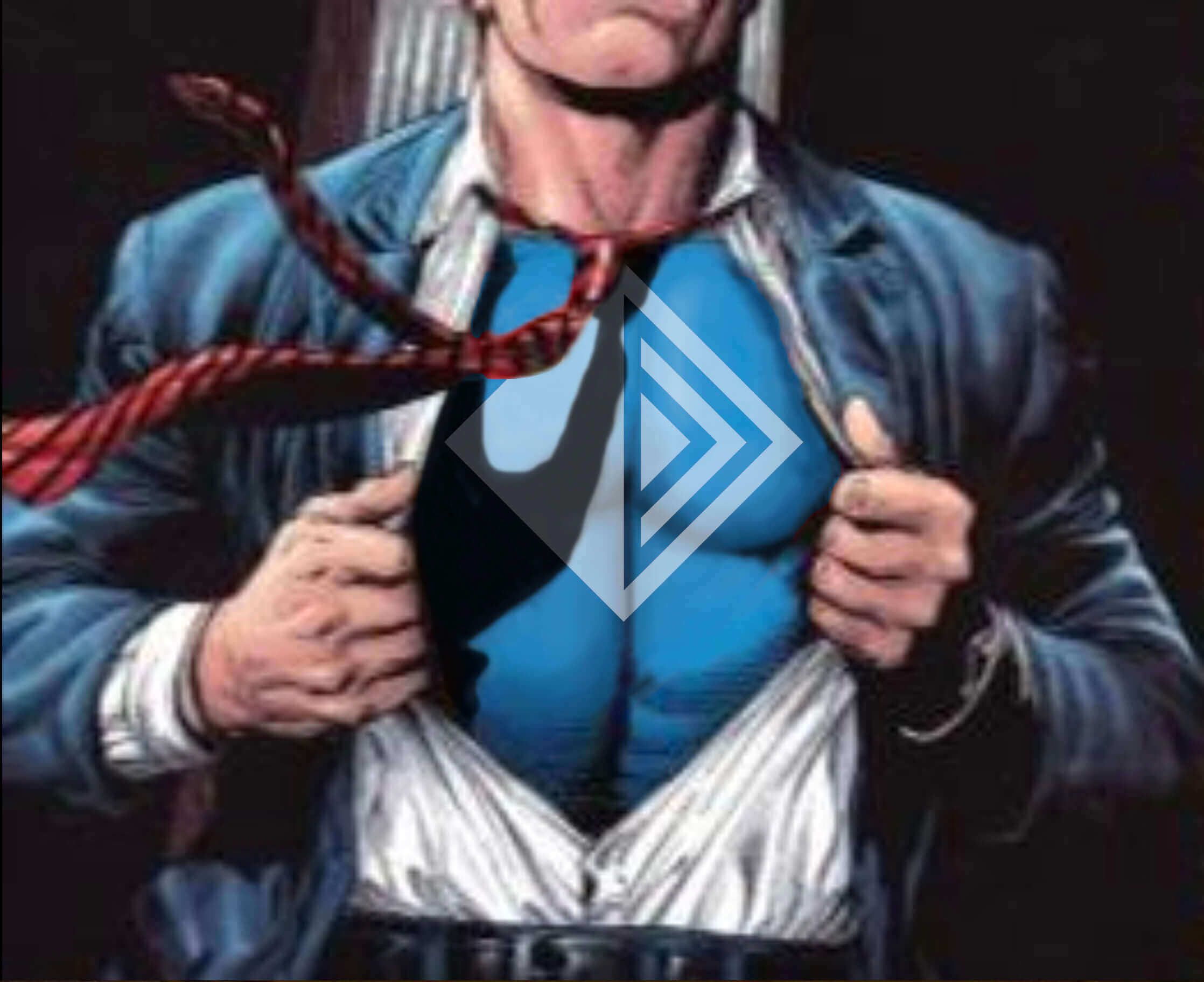
That’s how Telaeris likes to operate. We’re not lazy, but we believe in an efficient work environment and that it is always good to make life a little more simple. And it certainly feels great to be thought of as a superhero.
Testimonial
It is easy for someone to toot their own horn, but it is always nice to hear how the end customer felt – and the Marines were kind enough to give us their recommendations. Take a look at the video below to hear it in their own words. And if you want to improve efficiency in your business process, give us a call – we would love to help.