From 2015 through 2016, Telaeris executed a service contract with Marine Corps Base Camp Pendleton to assist the Marines with labeling 30,000 Base Property (BP) assets. The Marine Corps needed to achieve inventory accountability and visibility of property in accordance with Department of Defense (DoD) laws and regulations for resource management. This required working through their Accountable Property System of Record (APSR), the Defense Property Accountability System (DPAS).
When Telaeris arrived, the inventory process was manually labor-intensive and time-consuming. Telaeris was awarded a one-year contract solely to add manpower to the team of Marines who were currently walking the base, area by area, finding and tagging every asset they could find. The entire process was expected to take 2-3 years, and our contract had options for this renewal.
The reason Telaeris bid on this RFP was because we felt that our technology focus would allow our team to identify ways to improve the process. After all, with our XPressTools product, we had been doing asset management for years. But first we needed to understand the current process and challenges.
Assets being tagged
The assets on a Marine Corps base are varied, numerous, and widely spread out. Some of the assets we were tasked to find were:
- Computers/laptops
- Copiers
- Printers
- Televisions
- Appliances
- Trailers
- Lawnmowers
- Vehicles
- Historical weapons
The lists of these asset needed to be printed out, site by site from DPAS. These lists could range from 40 to 1000+ assets per site. The Telaeris team working with the Marines then needed to physically identify and tag all assets with current BP labels. And when the site was complete, a Custodial Assets Report (CAR) needed to be completed. On the CAR, we needed to identify which items were re-labeled and if any missing assets were reported. Broken or unused assets were turned into BP with proper paperwork for the Defense Reutilization and Marketing Office (DRMO).
Base Property’s Process
This was the standard approach of how base inventory was checked:
- 4 teams of 2 people divide the workload at BP. Each has multiple CAR accounts. BP would send a copy of the CAR to the Unit/Division and the Reporting Officer (RO) would track each Asset and its location. Then that Unit would make arrangements with BP to go out and tag/label their Assets.
- BP would pre-print labels identified on the Unit’s CAR the night prior to the site visit. Their pre-printed, yellow sticker labels came on a strip of perforated paper. Again, since CAR’s can range from 40 –1000+ Assets, this would equate to a strip of 40 – 1000+ sticker labels.
- At the Unit, an Asset would be located and the Serial number read out loud. Then the assistants would scroll through the strip of labels, find the matching label and stick it onto the top or front of the Asset. This completed the process of Asset being “tagged” and accounted for.
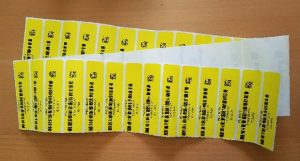
Complications
There were many complications to this process.
Human/Machine Error
Simple ones were based on human error – where the wrong list might be printed out for the site being visited. Unfortunately, since the base was so large, this could waste hours of a large team in terms of driving out to the site and returning for new labels.
Additionally, if the industrial label printer was broken, this would ground the asset team until it could be repaired.
Not all Assets Were Visible and/or Easily accessible
Laptops, most of the time, were with their user, which meant they might not be at the site. Computer Towers were hidden under, behind or on the side of a desk. Copiers/Printers were sometimes fitted into a space of convenience, above a desk or behind a door. With these assets, the issue was simply finding the asset and then locating the serial number.
Televisions provided one of the most time consuming challenges. These were mostly wall mounted without a swing arm. To read out the serial number, the TV’s needed to be unmounted from the wall, and then reattached. Appliances also needed to be physically moved to read serial numbers on their back sides.
Faded Printing
On Lawn Mowers and Vehicles, their Serial numbers were exposed to the elements and were often illegible.
Assets not on CAR but being used by Unit
Many times, sites would be in possession of assets that were assigned elsewhere. BP personnel would make notes and write down the Serial Number, Asset ID, Nomenclature, and location. The Base Property Team would take this info back to office and officially add to CAR, then return with printed label to tag Asset. This extra trip could take 2-3 hours in total of personnel time.
Telaeris’ Process
Telaeris was hired specifically to provide manpower to assist the Marines at BP to inventory all CAR accounts. For the first three months, our onsite team learned the Marine Corps process and spoke with Marines on the ground to identify what worked and what could be improved.
With this onsite intel, Telaeris engineers, back at our main office began to build a completely new system to expedite the asset tagging process. We realized that our system could not interface directly with government computer systems, but the result had to comply with all the regulations.
We were warned many times that any engineering efforts and equipment costs could not be charged back to the government. Also this effort could not affect our onsite work. Fortunately, as we had already built commercial inventory applications, most of the application was built quickly from existing pieces.
Enter XPressLabel
To meet these requirements, we built a system called XPressLabel. It consisted of:
- Custom written application
- Microsoft Surface Tablet
- Wireless label printer
- Wired barcode scanner
- Wireless barcode scanner
We tested the system at the office and when we were sure that it was ready, we demo-ed it to our Program Manager. He was so impressed that he approved our team using the system to speed up the asset tagging process.
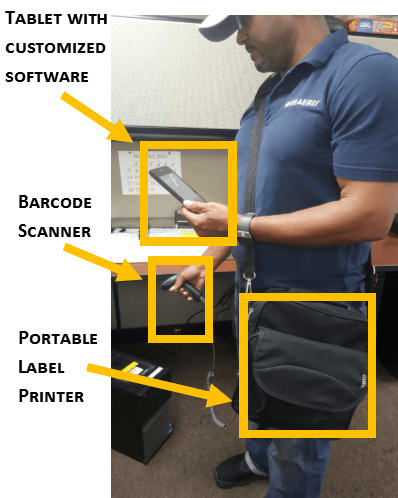
New and Improved Logistic Service Process
After we introduced the XPressLabel System, the process and program worked as follows:
- Unit’s CAR was downloaded onto Tablet. The CAR list was visible and searchable to provide accuracy, efficiency and to view the updated report as the day progressed.
- At the Unit, we located the asset, scanned the asset ID Barcode using the wired or wireless barcode scanner.
- The XPressLabel program confirmed the asset was on the CAR.
- When the operator has confirmed the asset, they tap the print button which initiates printing from the portable wireless printer.
- For hard to reach and illegible asset ID numbers, the scanners could read barcodes from up to 2 feet away.
- If only a partial asset ID number was visible, the program is able to search the CAR and filter down to determine if it is on the CAR or not.
- When unaccounted assets were found, the program provided the capability to add an asset onto a CAR, print a label and tag asset on the spot.
All of these provided great time savings. More importantly, it cut the number of people required for inventorying a site from 6-10 down to 1-2. Similarly, the time went down dramatically.
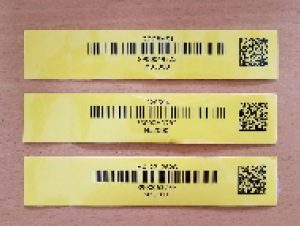
Outcome of Telaeris’ Logistics Service
The table below shows the time savings after implementing and utilizing Telaeris’ Logistics Service.
Activity Description | Before | After | Time Savings | # Per Area | Min Saved |
Preparation of labels and equipment | 30 min | 15 min | 15 min | 1 | 15 |
Accounting for item in DPAS list | 4 min
Manual locate & verify of asset id |
< 1 min
Barcode scanned & system verifies id |
3 min | 500 | 1500 |
Labeling items | 4 min
Go through label sheets |
< 1 min
Print label onsite with mobile printer |
3 min | 500 | 1500 |
Missing item procedure | 180 min
Mark item on list to update later |
5 min
System generates report of items found & missing |
175 min | 10 | 1750 |
List verification | 120 min
Manually go through paper list |
30 min
Electronically verified |
90 min | 1 | 90 |
Post reporting | 30 min
Manually enter report |
15 min
Export & import data |
15 min | 1 | 15 |
Telaeris’ service improved Base Property’s Inventory Process with efficiency and accountability. We achieved this by eliminating unnecessary printed labels for assets that were removed from CAR or going to DRMO. Also, by having the capability to add unaccounted assets on the spot, we were able to save time. Our service kept electronic form of an updated CAR with every asset added, label printed and not printed. Best of all, at the end of the day, an email with a report of the latest updated CAR was sent to the appropriate Base Property Team and Unit/Division RO for their records, making the team efficient with accurate information.
Most importantly, our system allowed the process to be completed in just over 1 year. While this may have lost Telaeris two years of contracted personnel at the base, it was the right way to serve our customer.
Please remember to read our accompanying blog article: The Lazy Man’s Approach to 10x Efficiency.
Leave A Comment